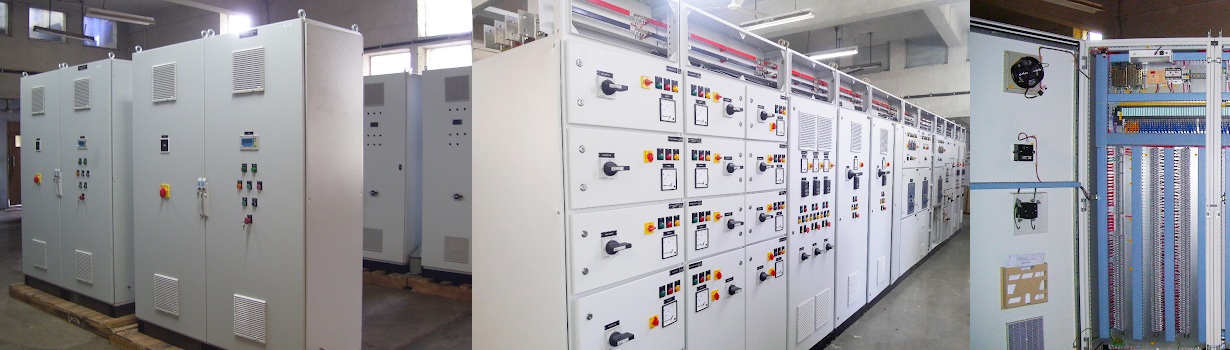
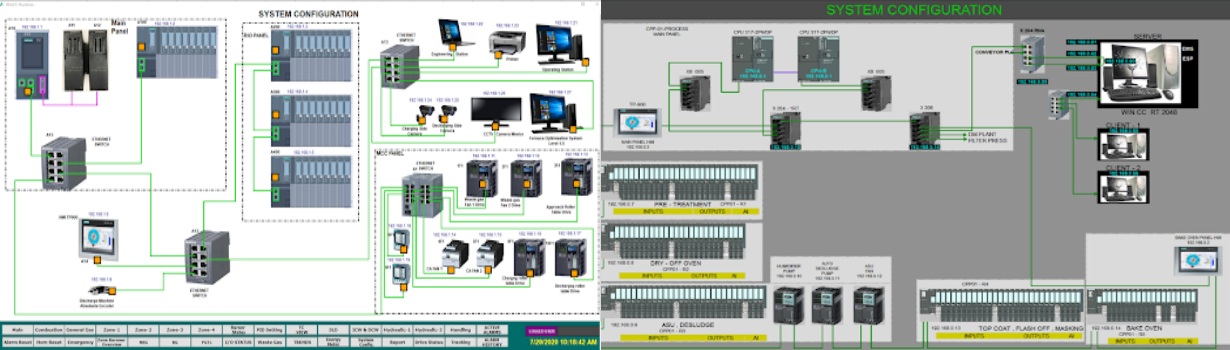
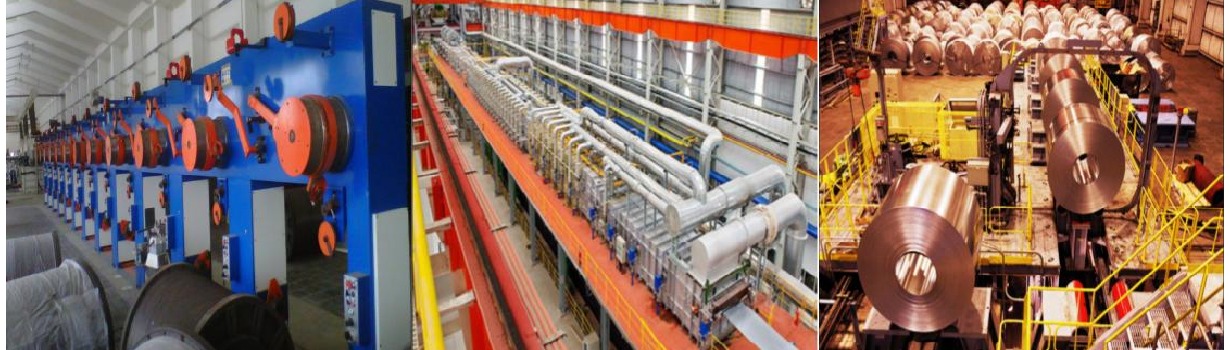
Automation
- Automation has revolutionized and continues to improve every area of application.
- The integration of transducers, input feedback signals, processors, power supplies, human machine interfaces and output Signals, with effective software at different levels, ensures that steps of the process are executed in a predetermined, predictable and optimized manner meeting process and machine requirements.
- Integration of plant data over cloud and remote monitoring with predictive management support in line with IOT 4.0
- Controls offered range from the Simple standalone to complex controls involving Fault Tolerant CPUs in redundant hot standby configuration with high levels of monitoring and integration with higher level systems and large amounts of secured data exchange.
- Appropriate sizing and application of complex Motion Controls with fast response times, and complete spectrum of variable speed drive applications
System Integration Strengths
- Range of controls offered is biased to more complex projects with large number of inputs and outputs, redundancy, fail safe applications, advanced Scada features, OPC connectivity, large and redundant communication networks while keeping the operation of the system simple and intuitive to use.
- Good understanding of system dynamics help us arrive at the optimum solutions for critical time dependent and synchronous operations through prime movers.
- Attention is paid to power system fault levels, graded protection and critical standby systems.
- Excellent documentation and training to end users, and adherence to international standards in design and manufacture ensures years of trouble free operation.
- We are ISO 9001-2015 certified company. Our systems compliant to UL508A (Certifcate No.20190313-E350288) for USA & Canada and CE (Safety and EMC compliance) for Europe.
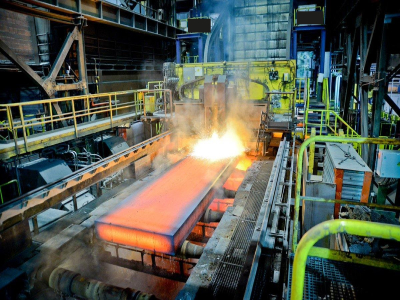
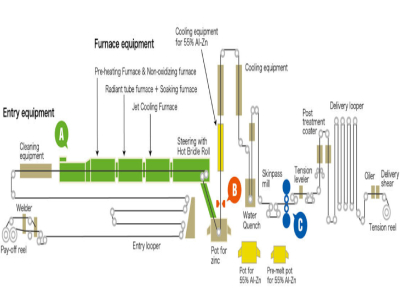
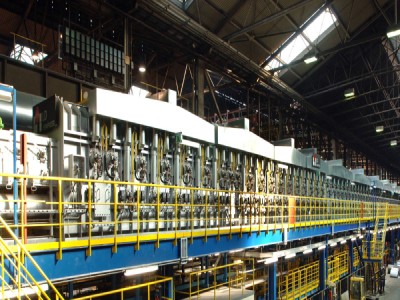
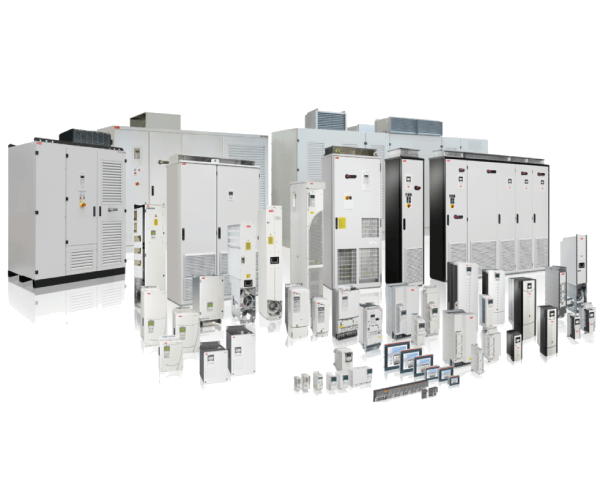
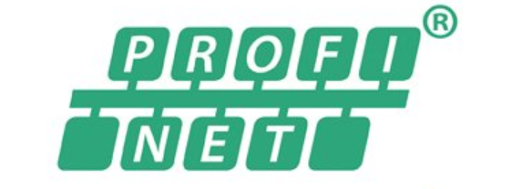
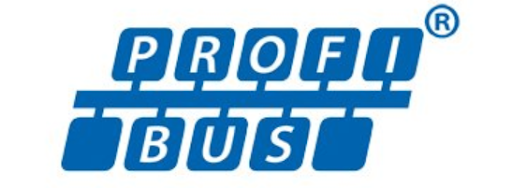
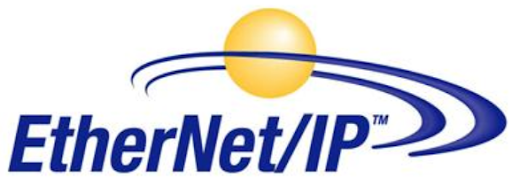
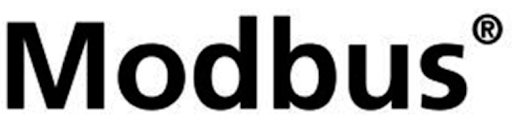
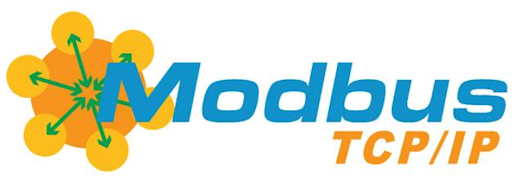
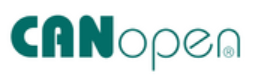
We continue to grow our team by actively recruiting and training resources on SIEMENS platforms, such as SIMATIC PCS 7, SIMATIC S7-200/300/300R/400/400F/H and TIA portal S7-1200/ 1500/1500R/H, WinCC as well as the legacy S5 Series platform.
We also offer complete variable frequency drive and servo systems (SIEMENS S120, G120 and ABB ACS 5xx/8xx) & commissioning.
Our team has a more comprehensive, deeper understanding of CPU Redundancy, IO Redundancy, SCADA interface to Plant DCS redundancies, SCADA Redundancy, Fail safe configurations to SIL2, SIL3 (1001) and (1002) configurations.
Automation solutions in Hazardous Areas like Zone-1 and 2
Vast Experience in configuration and implementation of Field bus protocols like Profibus, Profinet, Modbus, Modbus TCP/IP, Ethernet IP, Control net, Canopen.
With the features available in modern control systems, even complex advanced control strategies can be configured and programmed in these systems. Autodata provides design of integrated control system from field I/O's to MES systems.
Plants across a wide range of industries look to Autodata to provide additional staff support, maintenance expertise and the parts needed for these shutdowns. As part of our Field Services offering, we provide shutdown planning and services. Depend on us for the services, expertise and resources you need before, during and after an shutdown, helping you get back up and running on schedule.
Automobile | Paint shops, Test Beds for R&D and Production Lines, Rectifiers and Automation for CED. |
---|---|
Chemical | Sulphur Melting and Filtration, Chlorine Compressors, Batching plants. |
Furnaces | Ship Loader/Unloader, Engine monitoring systems. |
Nuclear | Waste recycling and disposal systems, Fuel bundle handling and inspection stations, Cobalt 60 Irradiation Plants for Pharma and Food. | Pharmaceuticals | High Speed Centrifuge controls, HMI solutions in Life science applications. Humidity control with our heater controls. |
Plastics | Blow moulding, Injection Moulding, Pre-form machines, Pipe Cutters, Pipe making . | Shipping | Ship Loader/Unloader with associated material handling, Engine monitoring systems. |
SPM | Press brakes, Material handling, Tube cutting, Electron Beam welding power supplies. |
Steel & Non Ferrous | Strip Processing lines like CGL, tension levelling, pickling, slitting, cut to length, continuous casting, Thin strip mills. Range of furnaces like Bell Furnaces, reheating, walking beam and hearth, hardening and tempering, homogenizing |
Tyre | Rubberizing Process Lines. | Wire and Cable | High Speed Insulating lines for Building wire, Fine Wire Drawing, Rod Breakdown, Drum Twisters, Stranding machines, coiling, extrusion lines, braiding, CV lines. |
Water | Storage and Distribution, RO and UV plants. |
Furnaces
- A bulk of these furnaces are used in the heat treatment of metals as in Roller and bogie hearth, bell Annealing, walking beam, Continuous galvanizing line furnace, Annealing and hardening furnace Continuous and batch processes.
- Furnaces can be oil, gas or Electric heated.
- Automation of these furnaces take into account the safety of operation, fuel/air ratio, burner management, zone wise cascaded temperature control, calculation based on heat flow and loss, thermal inertias, induced and forced draft blower control, recipe control of the temperature profile with respect to position and time, Optimization of throughput, reducing the heat loss during charge changes, recording performance and costs of operation, record of heat treatment processes, history, consolidation of multiple furnace outputs, and intimation of maintenance requirements, and connectivity to the cloud.
- Other aspects of control refer to the charging and discharging station control. There are also extensive programs for the tracking of the billets, coils, bundles as they are processed through the furnace, with a recording of the process they are subject to and to estimate when the output will be available for further processing such as rolling mills.
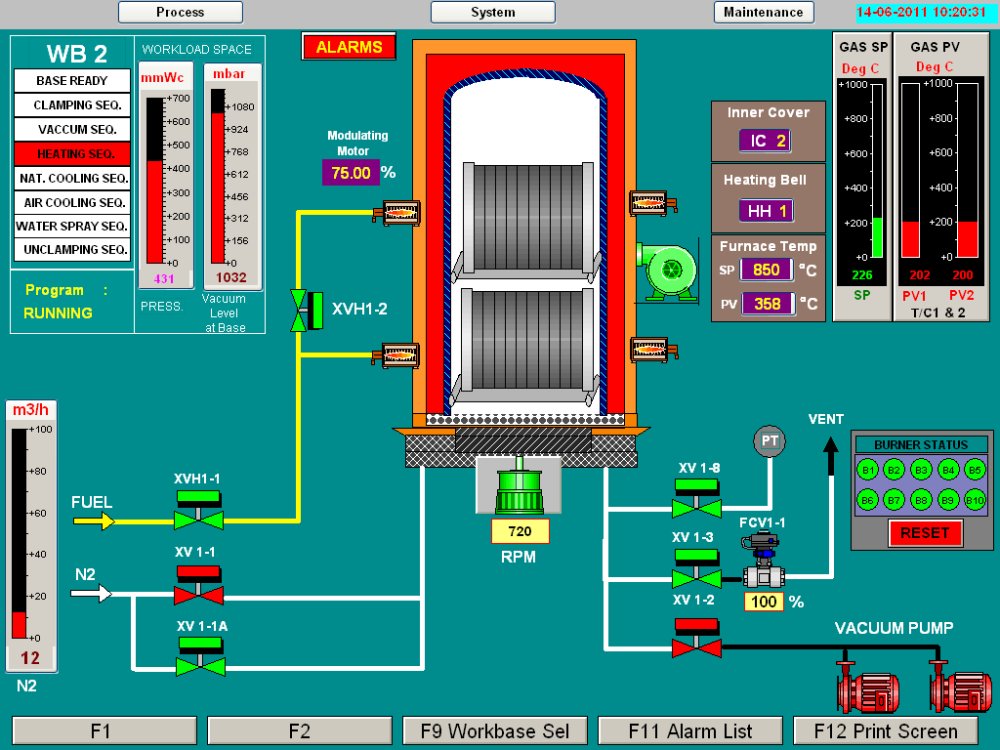
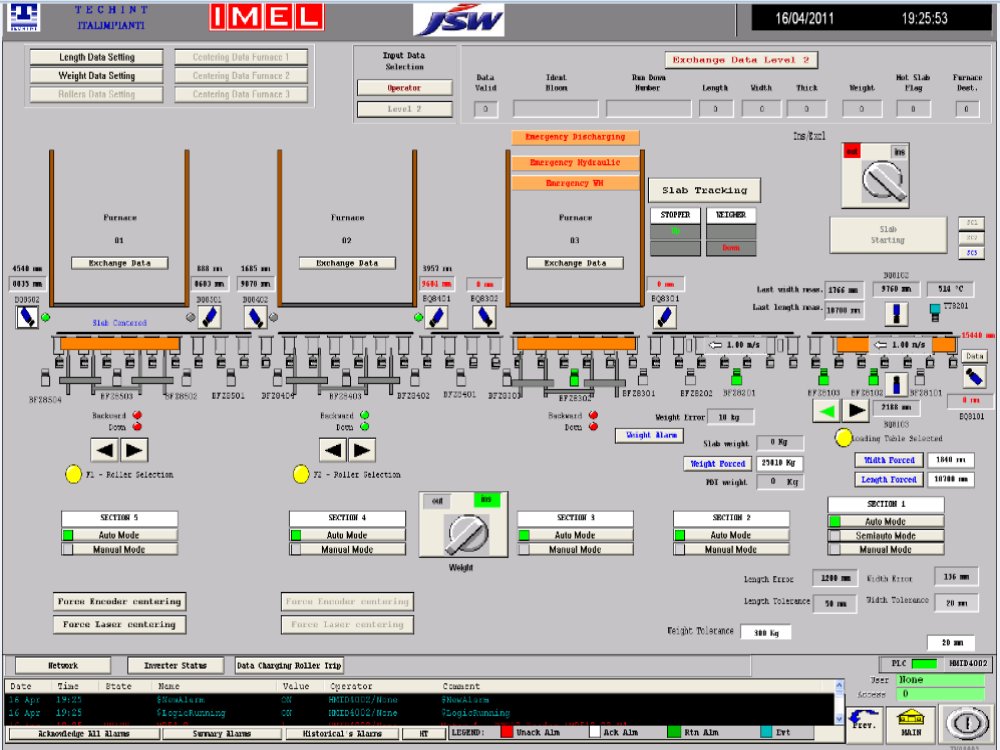
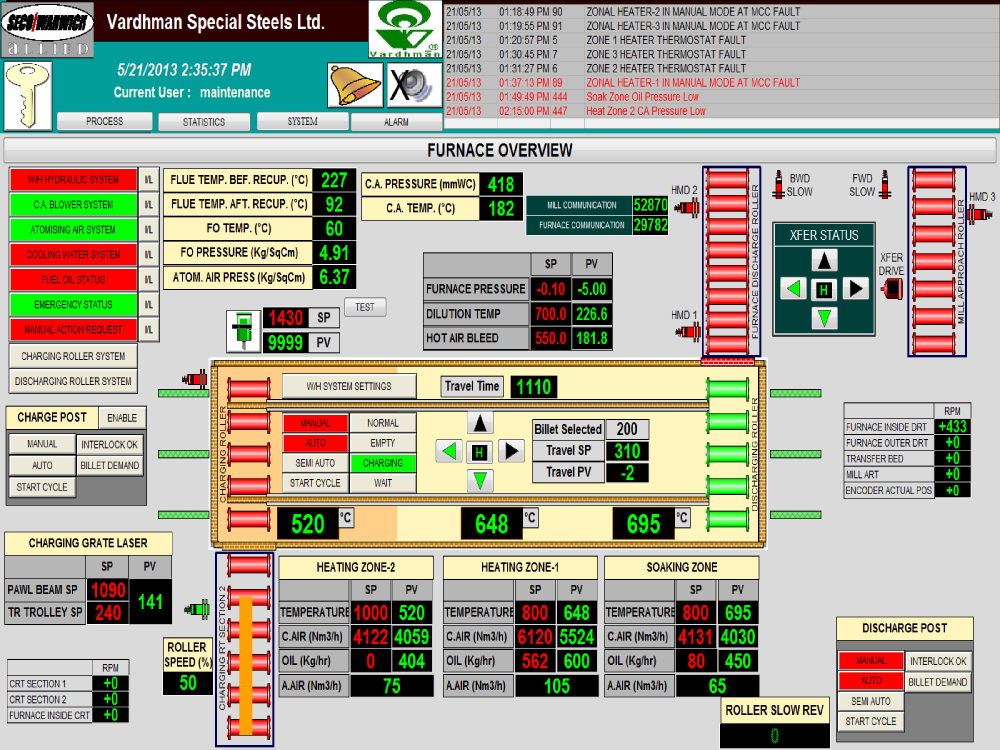
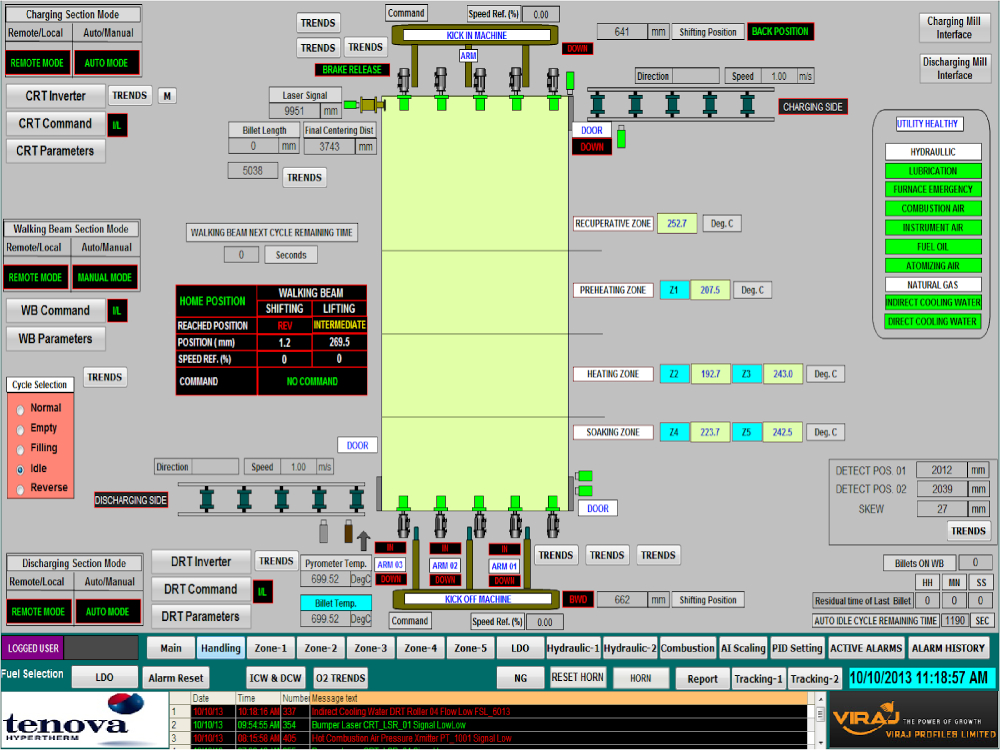
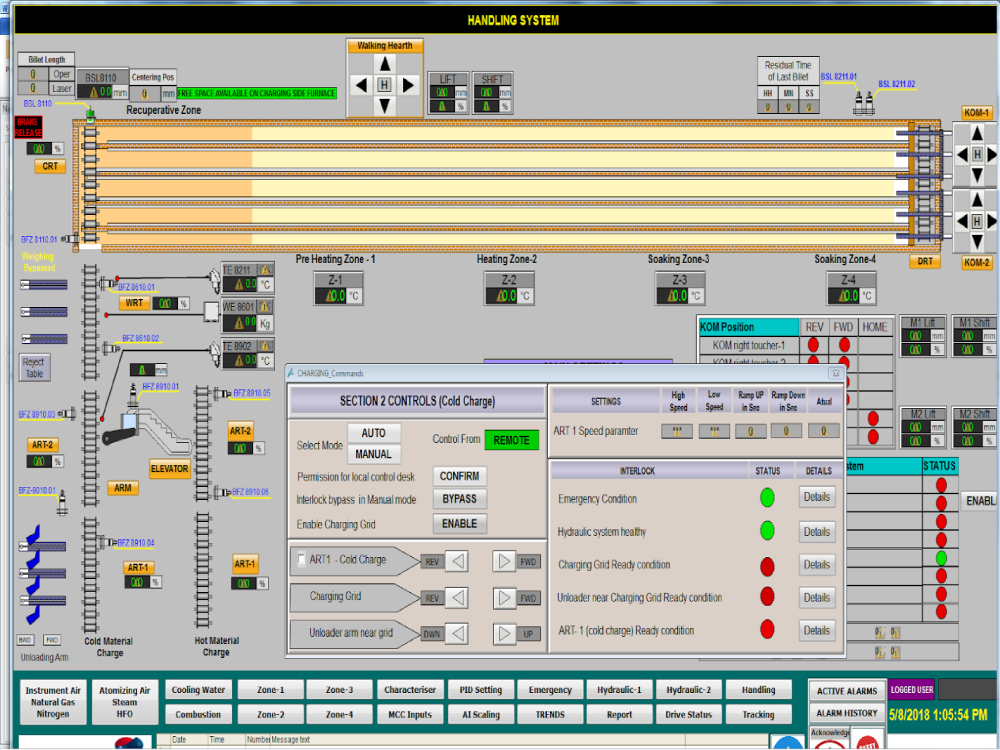
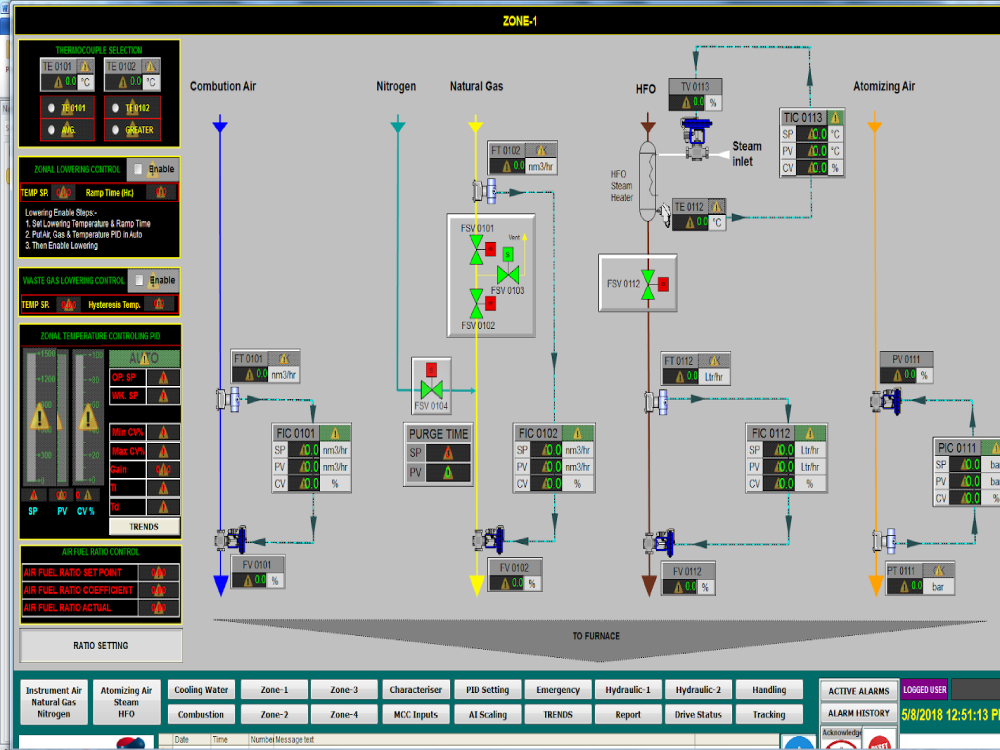
Automobile Factories > Paint Shop and conveyor Systems
Automobiles > Testbeds

Chassis dynamometer
Typically used to test the performance of vehicle, exhaust emission , fuel consumption, noise and fine tuning of exhaust and catalyst and motor fuel-injection system. Dynamometers simulate the real highway/ road driving conditions precisely. This requires that during acceleration and deceleration, the roll inertia be compensated dynamically , to match the mass of the tested vehicle and the real road. To be able to realize such high dynamic online compensation, the load torque of the roll motor is controlled accurately and with extreme precision at every speed point.Chassis dynamometer for two wheelers , three wheelers , four wheelers delivered.

Engine test stands
To measure power and torque directly from the engines crankshaft means knowhow in the selection of a correct AC machine with proper electrical and mechanical characteristics like smaller leakage inductance and inertia , and fast torque response management are challenges we are aware off and successfully delivered high performance test stands . Torque rise times achieved 1-2millisecs. On the fly bump-less switch between Speed/Torque , Torque/Speed. Up-to 10000 RPM Max speeds

Transmission and clutch Test Stands
These stands include several motors — one simulating engine, and two or more to simulate the road. This requires mutual coordination of drives operation, the faster and more accurate it is the better it simulates real-world conditions like differential gear operation. Uphill/Downhill drive modes . Up-to 10000 RPM Max speeds

Atomic Energy-Gamma irradiation plant controls
A number of times in close coordination with the OEMs and the Atomic Energy Regulatory Board. Incorporation of very high levels of safety, 21CFR US FDA compliance.
- Gamma irradiation plant controls for the irradiation of medical products, agriculture produce such as Onions and mangoes, surgical gloves and accessories, necessities, with the attendant safety, material transport and ensuring the elimination of pathogens have been done
- ADFTS Automatic Direct Bundle transfer system
- Pellet inspection systems
- PHWR Special purpose automatic energy bundle inspection system
- Special programmed ovens
- Glass heating systems for encasing for atomic waste disposal units.
- Transport systems for Container Inspection systems

Wire and Cable Machinery Control
Controls for a range of machinery from Rod Break down, Intermediate wire drawing, fine wire drawing, In line annealing, Insulation lines, Extrusion lines for cables, Bunching and stranding machines, Vulcanising lines, High voltage cable lines, Mixers, pay off and take up winders, These lines involved coordinated variable speed drives. Temperature control and heater control, sequence logic and safety systems, diameter sensors, speed correction algorithms

Strip Processing Lines
Steel and non ferrous strips slitting, cut to length, leveling, tension leveling, accumulators, bridle rolls, un coilers, coilers, weld detection. Automatic change over of pay off coils. Forming mills that process strips and form them into the required shapes in successive stands need coordinated drive systems and dancer control. These controls include welding rod production units with material filling, card clothing side strips etc. Complete paper and board plants, slitting lines, flying shear cut to length lines.
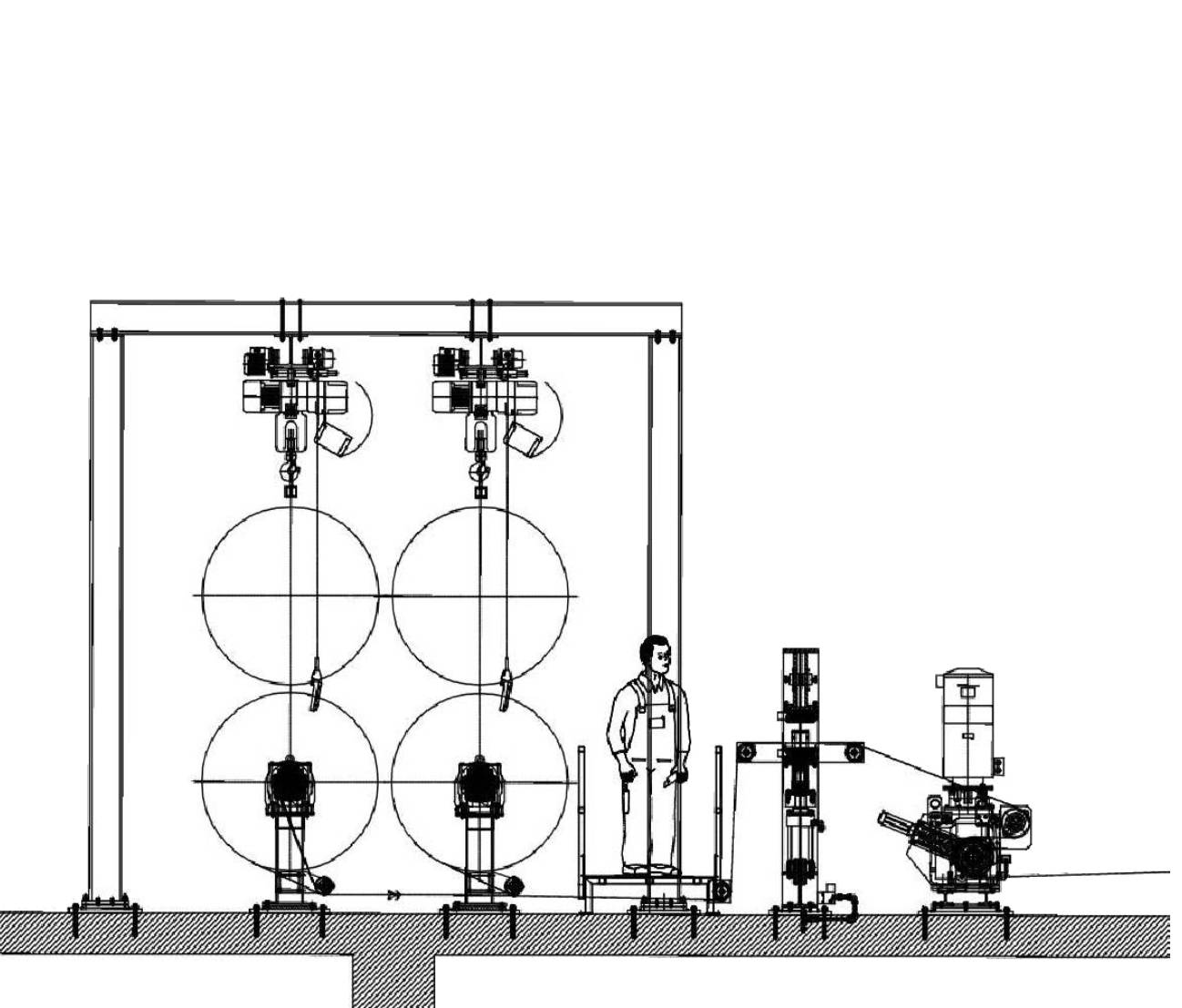
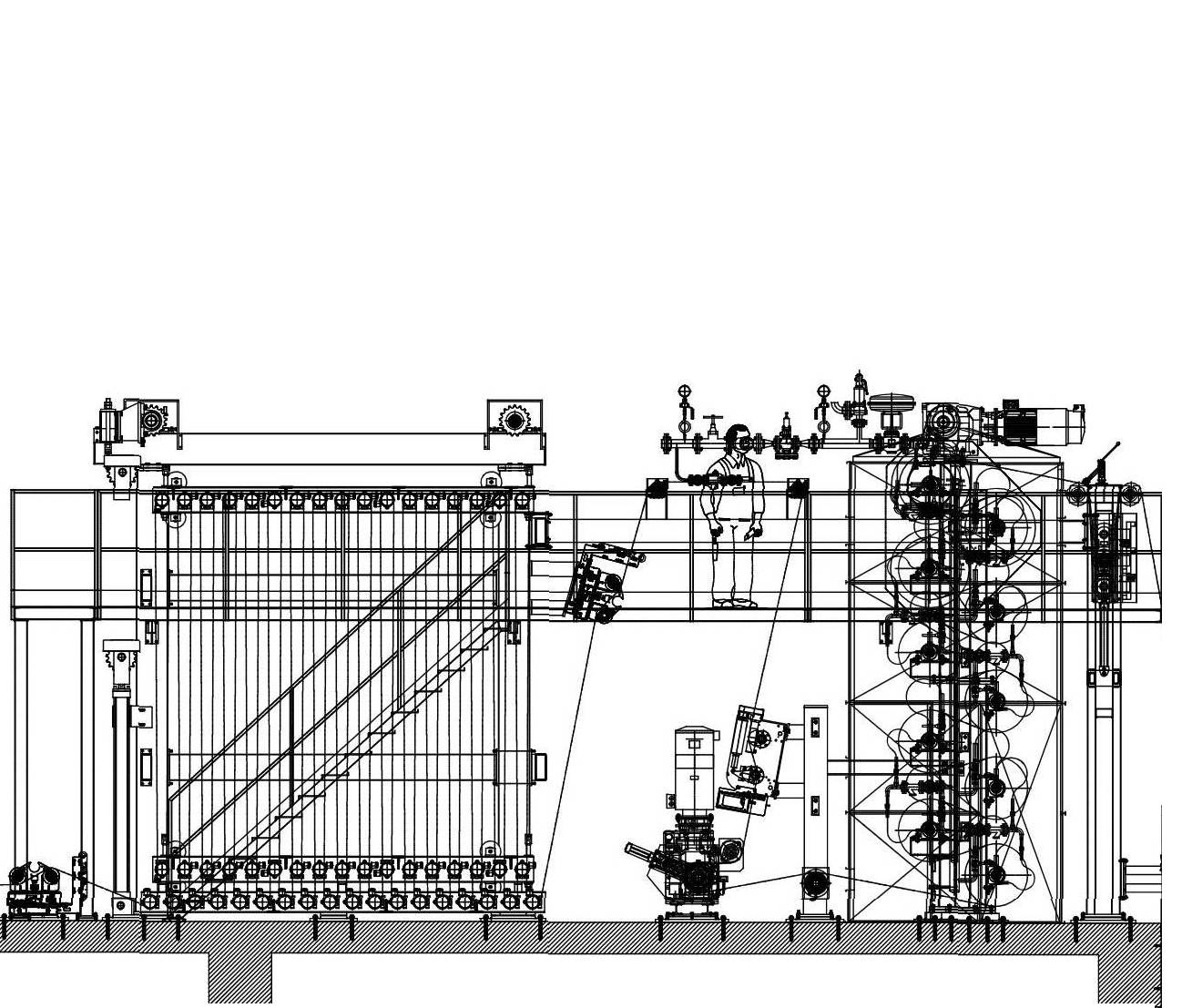
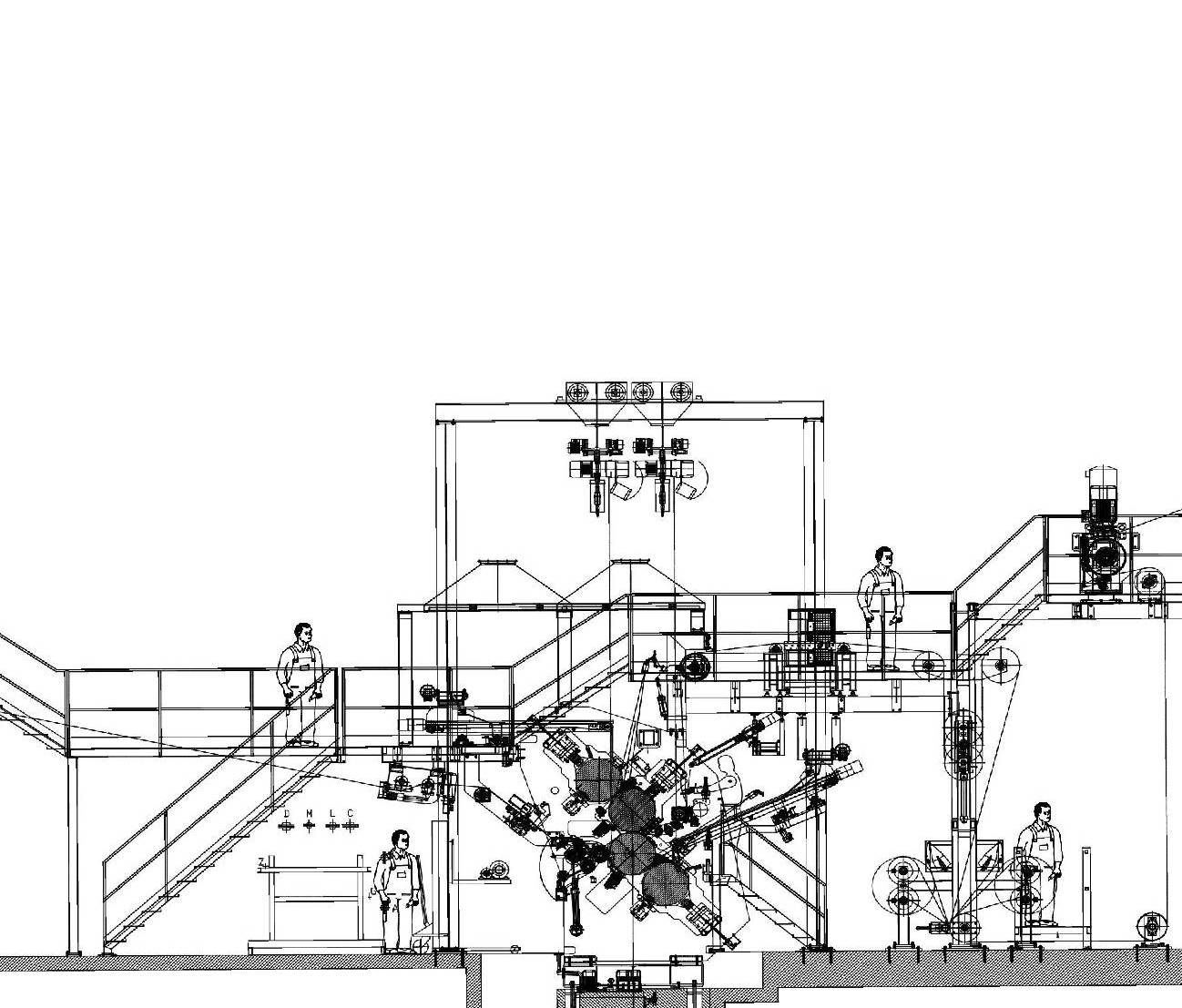
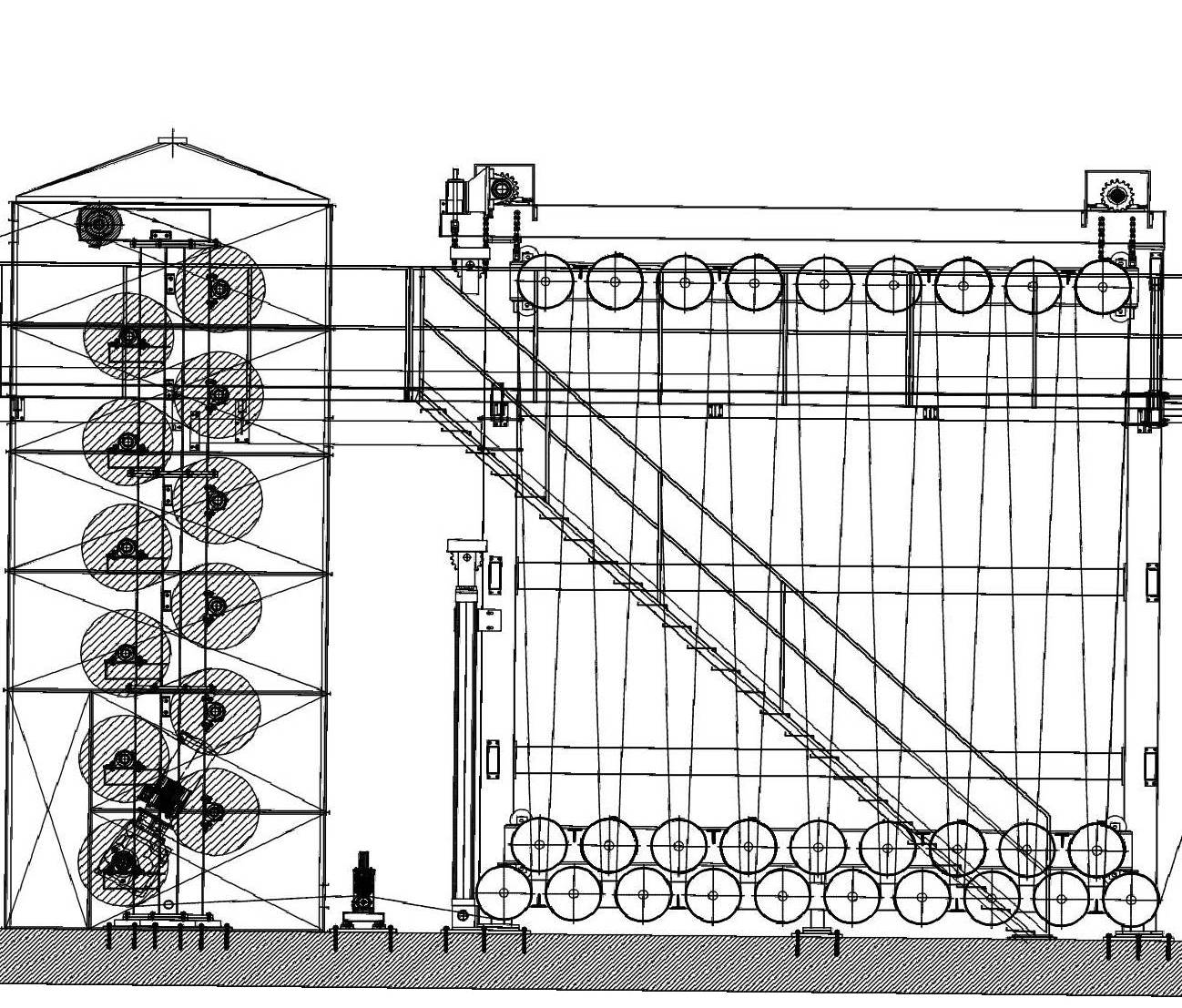
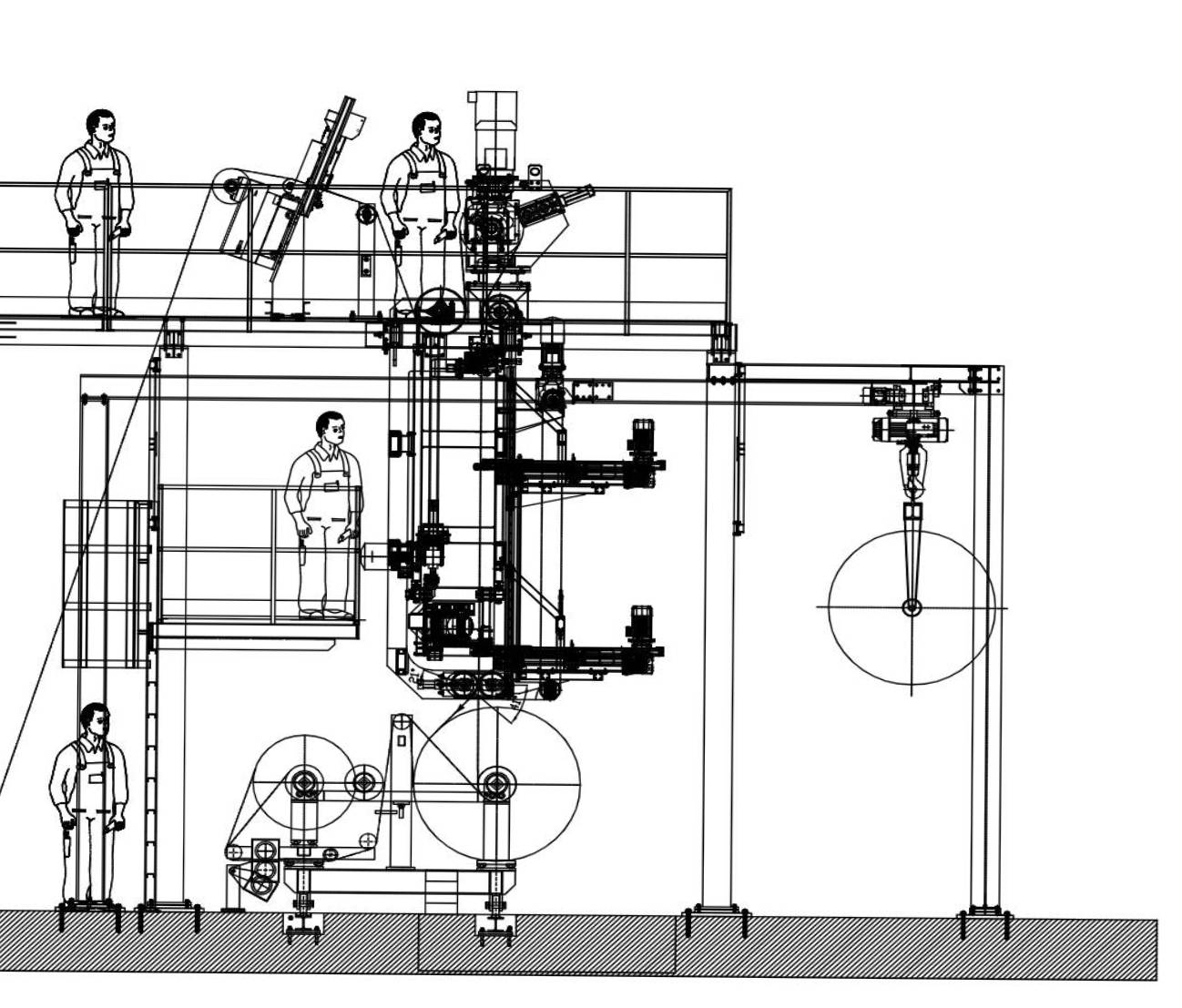